Rotary Kiln
Rotary kilns are cylindrical devices widely used in various industries for thermal processing applications.They are capable of achieving high temperatures while continuously rotating, allowing for the efficient processing of materials.From cement production to waste incineration, rotary kilns play a crucial role in transforming raw materials into valuable products.
Rotary kilns are cylindrical devices widely used in various industries for thermal processing applications. They are capable of achieving high temperatures while continuously rotating, allowing for the efficient processing of materials. From cement production to waste incineration, rotary kilns play a crucial role in transforming raw materials into valuable products.
The structure of rotary kiln body:
Our rotary kiln include Shell,Refractory Lining,Support Rollers,Gears and Drives,Feed End,Discharge End.
Based on the functions of each section, the rotary kiln body is divided into 4 sections: Feeding, Heat Application, Rotation, Processing, and these 4 sections are connected together.
The shell is the outer cylindrical structure made of steel. It is lined with refractory bricks to withstand high temperatures. The refractory lining is the inner layer of heat-resistant material that protects the shell from direct heat exposure.The support rollers: are wheels that support the kiln and allow it to rotate.The gears and drives are mechanisms that enable the rotation of the kiln.The feed end is where the raw materials enter the kiln.
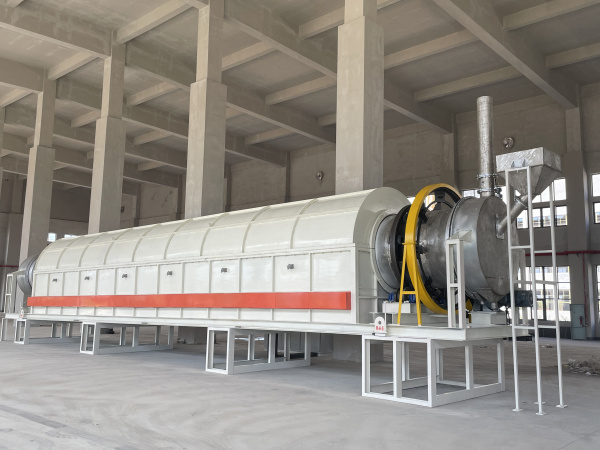
Characteristics of rotary kiln
- 01 Rotary kilns are designed for continuous operation, which means they can process materials without interruption. This feature is critical for maintaining high production rates and ensuring a steady supply of processed materials.
- 02 Rotary kilns are versatile materials handling tools that can efficiently process powders, granules or larger lumps. They are used in a variety of industries including cement production, mineral processing and waste management.
- 03Rotary kilns allow for precise temperature control, which is critical to ensuring that materials undergo the desired chemical transformation at a specific temperature. Maintaining consistent temperatures throughout the kiln ensures that the final product meets quality standards and specifications.
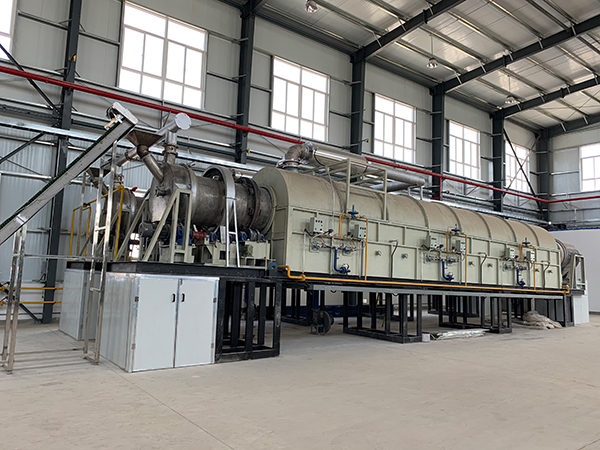
- A Feeding:
- B Heat Application:
- C Rotation:
- D Processing:
- E Discharge:
-
A
Feeding:
The raw materials enter the feed section of the rotary kiln from the feed inlet. In this section, the raw materials are evenly distributed over the entire cross-section of the kiln barrel.
-
B
Heat Application:
In this area, the raw materials undergo a high-temperature heat treatment process. Through the performance provided by the combustion equipment, the combustion gases generated in the burner heat the materials in the kiln.
-
C
Rotation:
A driving device is installed in the kiln to rotate the kiln barrel along the horizontal axis and move the material to the discharge end.
-
D
Processing:
The calcining section located after the feeding section is a key part of the rotary kiln. The high temperature and rotational motion of the kiln barrel make the material quickly reach the required reaction temperature and maintain good contact between the material and the combustion gas to achieve calcining or sintering of the material.
-
E
Discharge:
After the material is calcined, it is discharged from the discharge port of the rotary kiln. A suitable discharge device will be set up to control the flow and discharge speed of the material.
The advantages of rotary kiln :
-
01
Continuous Operation:
Rotary kilns are designed for continuous operation, ensuring a steady throughput of materials. The rotary kiln has the ability to continuously feed and discharge materials, and the production process is uninterrupted.This feature is particularly advantageous in industries where consistent production is essential.
-
02
High Temperature Capability:
These kilns can reach extremely high temperatures, It can withstand high temperatures of thousands of degrees Celsius and is not easy to deform and crack.often up to 2000°C (3632°F), This high temperature resistance enables the rotary kiln to maintain a stable structure during the calcining process, ensuring the calcining effect.making them suitable for demanding thermal processing applications such as cement production and metal smelting.
-
03
Versatile Material Handling:
The rotary kiln can handle a variety of materials, including ores, garbage, chemical waste, etc., from powder to granules and blocks. Its high temperature and uniform temperature field make it suitable for the calcination and incineration of various materialsand are effective in processing both wet and dry materials.
-
04
Precise Temperature Control:
The rotary kiln is equipped with an advanced temperature control system, which can achieve precise adjustment and stable control of the temperature in the kiln, helping to ensure the stability of the process and product quality. This precise temperature control provides reliable control for experiments and production. Assure.
-
05
Customizable Design:
The rotary kiln can be customized according to different production needs to meet diversified production needs. It can also be designed and adjusted according to different material characteristics to ensure that the materials can roll forward evenly in the kiln and be heated evenly, making it highly adaptable to different materials. industrial requirements.
-
06
Energy Efficiency:
Modern designs incorporate energy-efficient features, The rotary kiln has better energy utilization and higher heat transfer efficiency. At the same time, it can be adjusted according to the characteristics of the material and heating requirements to avoid energy waste, such as recuperative preheaters and waste heat recovery systems, which help reduce fuel consumption and operating costs.
-
07
Ease of Maintenance:
The rotary kiln has a reasonable structural design and excellent material selection, which makes it have a long service life. At the same time, the repair and maintenance of the rotary kiln is relatively simple, the failure rate is low, the daily maintenance workload is small, its internal components are easy to access, and the modular design facilitates repair and upgrade, thus reducing maintenance costs.
-
08
Robust Construction:
The solid structural design enables the rotary kiln to operate stably in high temperature, high pressure and corrosive environments, ensuring the continuity and efficiency of the production process. Material selection is also important. The shell is an external cylindrical structure made of steel, and its inner Lined with refractory bricks to withstand high temperatures and provide long-lasting durability even under harsh operating conditions.
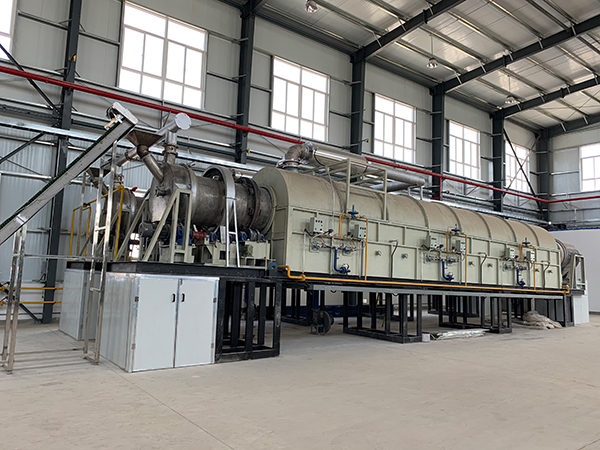
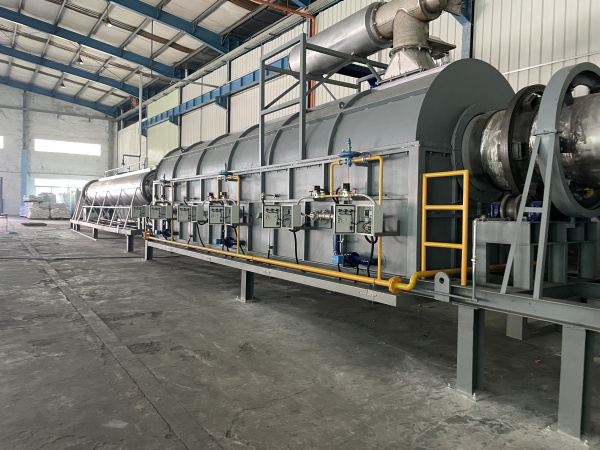
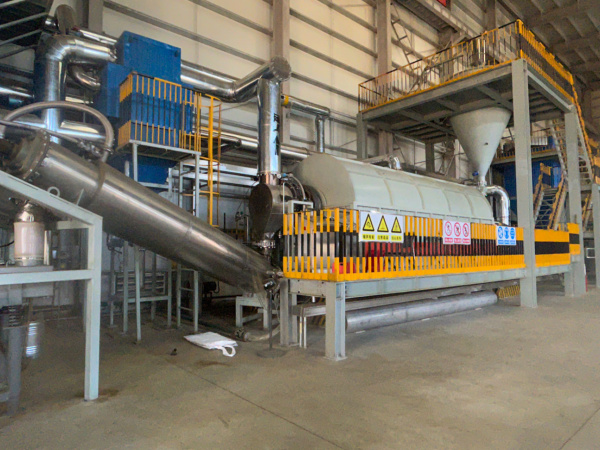