Prefabricated Tunnel Kiln
The high mechanization and automation function of tunnel kiln make the production process of brick making enterprise produce a tremendous change, greatly changed the working condition of workers, reduced the labor intensity of the operator, make the brick making enterprise become the enterprise truly, and it is the enterprise with better economic benefit.
The structure of prefabricated tunnel kiln body:
Prefabricated tunnel kiln refers to the kiln body of a large cross-section tunnel kiln, which has several kiln car tracks and kiln cars for synchronous drying and roasting. The kiln body can be designed with multiple assembly types such as double assembly, three assembly, four assembly, and five assembly.
Prefabricated tunnel kilns are suitable for using various solid waste materials such as construction waste, urban sludge, construction waste, environmentally friendly sludge, industrial tailings, and coal gangue as raw materials for brick making. It has a wide range of sintered products, including various types and specifications of new wall materials such as standard bricks, hollow bricks, insulation bricks, etc.
Our company's advanced design and energy-saving concept for prefabricated tunnel kilns are the first in the country. Our mature technical solutions and continuous self-improvement have won recognition from experts and peers in the wall material industry, and we are at the forefront of similar kiln enterprises in the wall material industry.
Characteristics of Prefabricated tunnel kiln
1.Adopting a large cross-section design, industrialized and modular production.
2.The double sealing design eliminates the need for multiple side kiln walls, reducing the heat consumption of each side kiln wall by 8%.
3.The use of a new rapid drying system has solved the production and production difficulties of high moisture content raw materials.
4.High degree of automation, application of 5G technology and central control room, digital roasting control, reducing the impact of human factors.
5.The kiln design uses international large-sized steel to ensure the overall structure of the kiln is sturdy and durable, saving maintenance costs.
6.The use of a flue gas reburning system for secondary utilization of flue gas reduces the processing capacity and oxygen content of the discharged flue gas, which is beneficial for achieving emission data standards.
-
Drying section
The drying kiln adopts a double door design, utilizing the heat and waste heat of the roasting kiln for further dehydration and drying. The high oxygen content flue gas is discharged and sent to the cooling and insulation section for oxygen supply and re firing through the "flue gas re firing system". The discharged high-temperature flue gas is sent to the flue gas treatment system for purification treatment. After drying, the bricks are sent to the roasting kiln.
Baking section
The calcining kiln adopts a double gate design to ensure a more stable airflow inside the kiln. During the walking process inside the calcining kiln, the kiln car goes through preheating, calcining, insulation and cooling processes in sequence. The kiln car adopts a "double channel sealing design" to ensure smooth and reliable operation.
Comparison of performance between fabricated tunnel kiln and ordinary tunnel kiln:
-
01
Working system
In addition to the working system of the ordinary tunnel kiln, the prefabricated tunnel kiln also has a multiple fuel combustion coexistence system in the firing area of the kiln, which burns multiple fuels without changing the structure of the tunnel kiln. Ordinary tunnel kilns are difficult to change their combustion methods and have poor combustion stability, while prefabricated tunnel kilns can easily convert into the fuel used for combustion, or the proportion of solid fuel to liquid fuel, or the proportion of solid fuel to gas fuel.
-
02
Sealing performance
The ordinary tunnel kiln is constructed by kiln workers using refractory bricks, insulation materials, and building materials. The sealing performance of the kiln is related to every brick laid by the workers. But the assembled tunnel kiln is different. It uses standard molds, selects the same materials according to the same technical requirements, and assembles tunnel kiln parts into standard parts in the factory. Each standard component has accurate dimensions and the same quality, making it easy to install the gap between two standard components in a unified form for processing, ensuring the sealing performance of the tunnel kiln wall and roof.
-
03
Insulation performance
The inner layer of the ordinary tunnel kiln wall is made of refractory bricks, the middle insulation layer is made of lightweight refractory bricks and insulation felt, and the outer layer is made of building bricks. The inner layer of the prefabricated tunnel kiln is made of high-temperature resistant materials. Experiments have shown that under the same surface temperature of both kiln walls, the heat dissipation of the prefabricated tunnel kiln wall is only 1/4.1 (24.3%) of that of the ordinary tunnel kiln wall. Therefore, the insulation performance of prefabricated tunnel kilns is far superior to that of ordinary tunnel kilns.
-
04
Construction period
The basic construction period of ordinary tunnel kiln and prefabricated tunnel kiln is basically the same, because prefabricated tunnel kiln is lighter in weight, the foundation is slightly smaller, the foundation construction can shorten some days.Above the foundation, the ordinary tunnel kiln needs about 50 construction workers, which can take 70-80 days to complete the construction, while the assembled tunnel kiln only needs about 20 construction workers, and most of them are general workers. The construction can be completed in 30-40 days, and the construction personnel and construction cycle are less than half of that of the ordinary tunnel kiln.The technical personnel required for the construction of the assembled tunnel kiln is only a fraction to a tenth of the technical personnel required for the construction of the ordinary tunnel kiln.
-
05
Construction cost
In terms of construction personnel costs, ordinary tunnel kilns use many skilled workers, and the construction period is longer, resulting in higher construction costs. For the material quantity of the structural part, prefabricated tunnel kilns are 30-40% more than ordinary tunnel kilns. Therefore, the material construction and transportation costs of prefabricated tunnel kilns are higher than ordinary tunnels. The processing cost of processing workpieces is also higher than that of ordinary tunnel kilns. After making up for the difference, the overall cost of assembling the tunnel kiln is slightly higher, mainly due to the better materials used in the prefabricated tunnel kiln.
-
06
Flexible performance
Once a ordinary tunnel kiln is built, it cannot be moved or dismantled or rebuilt elsewhere. The prefabricated tunnel kiln is detachable and can be disassembled into standard components according to the opposite operation of installation, and then reinstalled if necessary, allowing for normal use. If the kiln wall of a ordinary tunnel kiln is damaged, production can only be stopped and maintained after the temperature of the kiln has decreased. But when the kiln wall of the prefabricated tunnel kiln is damaged, there is no need to stop production. Simply remove the damaged part and replace it with a new one.
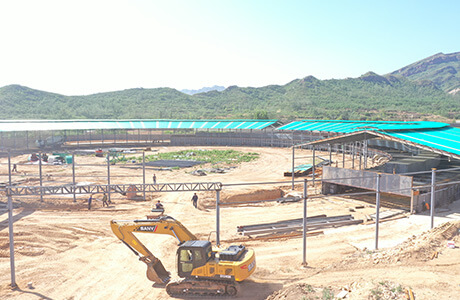
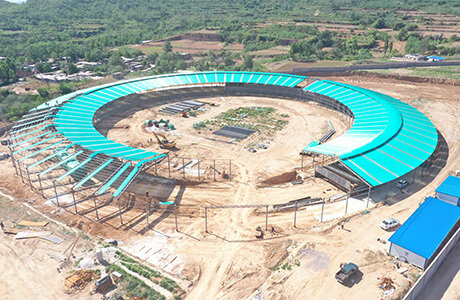
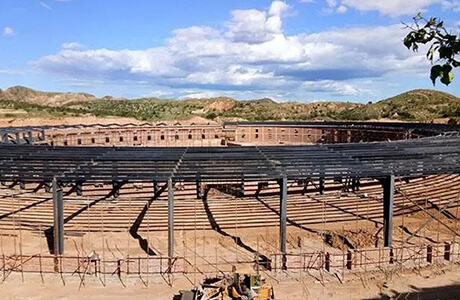
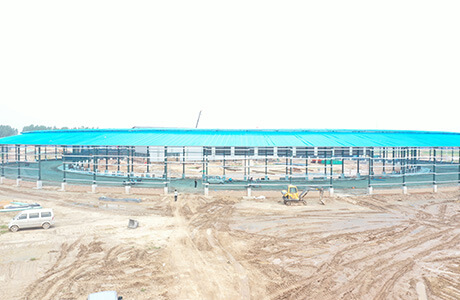
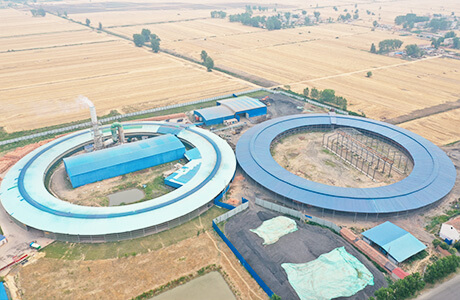
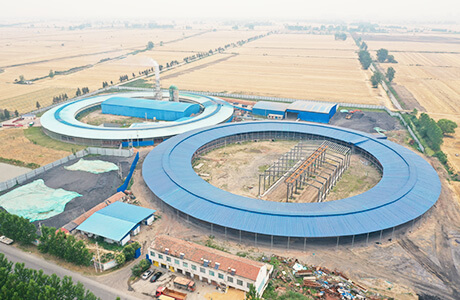
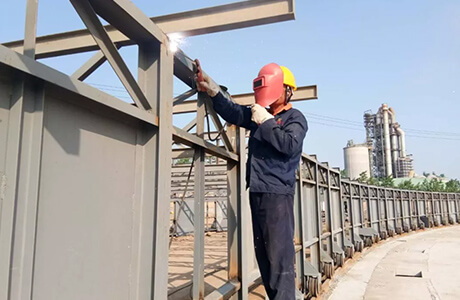
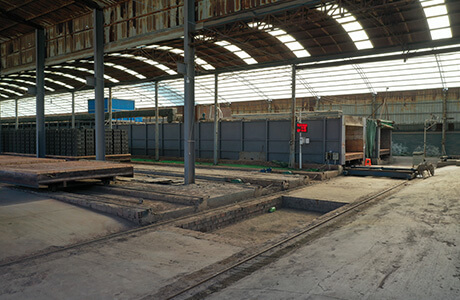