Parallel Tunnel Kiln
The clay bar machine after forming is sent to the blank cutter, which is cut into the required size of the blank. Then it is sent to the kiln car by the blank distributor, the blank conveyor, the automatic blank code machine, and sent to the blank shop by the hydraulic ferrying machine for storage.The brick dried by air is sent to the drying kiln by the hydraulic ferrying crane.
Type of kiln: Parallel Tunnel Kiln
For the raw materials with high plasticity index and high drying sensitivity coefficient, it can be arranged as one burning and two drying in parallel to ensure the drying quality of the blank.
Since the drying chamber is under full positive pressure, the cold air from outside is prevented from invading the chamber, and the drying process is less affected by the environment and climate.
Dispersed air supply and dispersed moisture discharge, which can flexibly adjust the air supply and moisture discharge. Therefore, the cross section temperature of the drying chamber is more uniform, and the dry quality of the blank body is good.
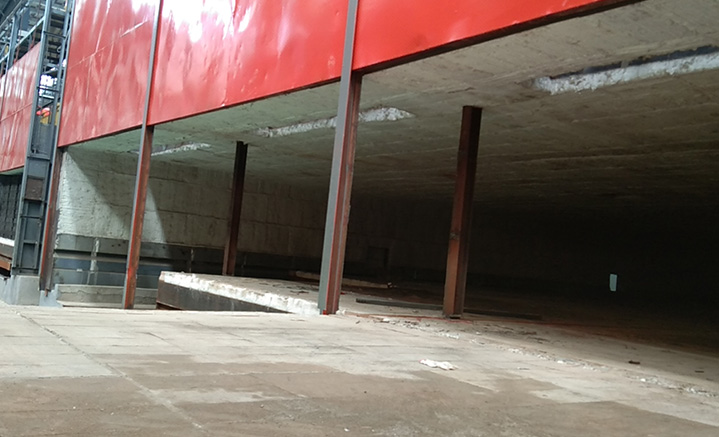
Characteristics of a Parallel Tunnel Kiln
- 01 Less investment, material province, save investment half.
- 02 Adequate dry heat, qualified rate of more than 99 %.
- 03 The product quality is excellent, the calcination is even, the yield is high.
- 03 Low heat consumption, roasting temperature 1100°.
Production Process of Parallel Tunnel Kiln body:
-
Drying and moisture eliminating section.
The clay bar machine after forming is sent to the blank cutter, which is cut into the required size of the blank. Then it is sent to the kiln car by the blank distributor, the blank conveyor, the automatic blank code machine, and sent to the blank shop by the hydraulic ferrying machine for storage.The brick dried by air is sent to the drying kiln by the hydraulic ferrying crane.
-
Preheating section.
The dry heat source of the brick comes from the roasting section. The waste heat is extracted by an induced draught fan and sent to the drying room for drying.
-
Burning section.
After the kiln truck is finished unloading the bricks, the return line is returned to the preparation place of the blank code machine through the process, and the blank code is carried out again.
-
Cooling section.
Dry and burn.The drying and firing process is carried out by the one-step code firing process. The drying and firing kilns can be arranged in one font or parallel parallel position according to the requirements of the production site.The burning fuel is mainly internal combustion of fly ash, supplemented by external coal injection.
-
1.Continuous production, short cycle, large output and high quality.
-
2.Integrate automation, digitalization, humanization and systemization into one
-
3.The investment is small, and the total investment is more than 50% less than that of a tunnel kiln of the same cross-section.
-
4.It has good energy-saving effect. It uses special high-temperature-resistant insulation materials and makes full use of thermal energy to reduce heat loss.
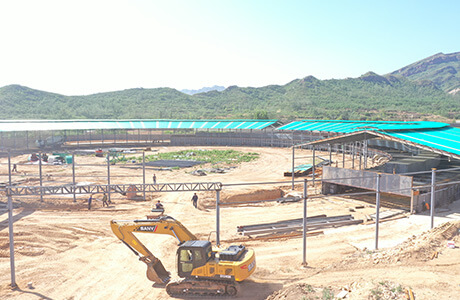
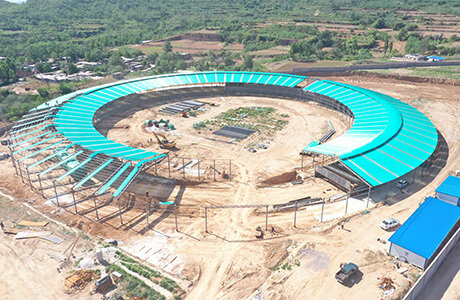
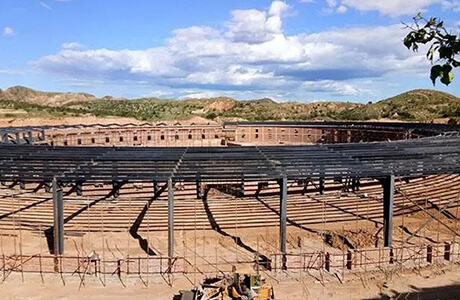
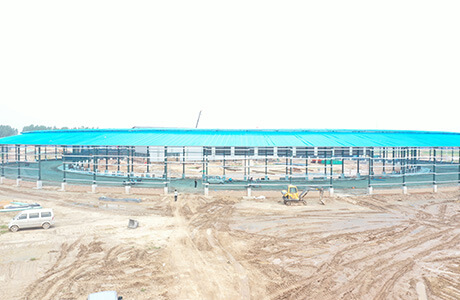
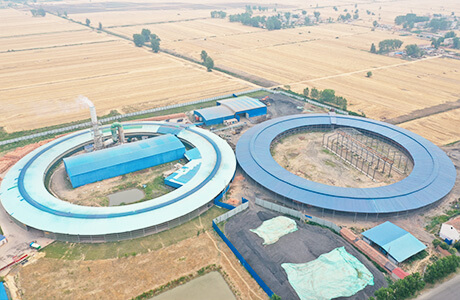
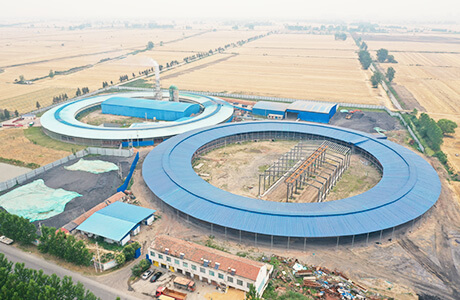
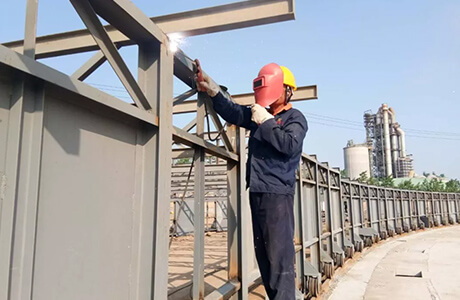
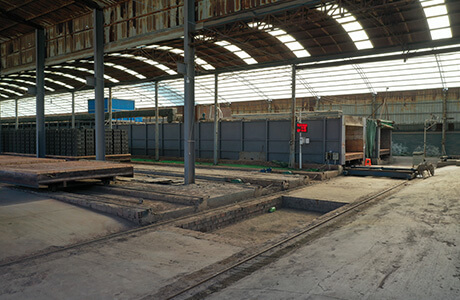